Continuous loading and the impact on your operation.
If you do what you always did, you will get what you always got.

Changing the current way of Drill & Blast decline or development operations towards continuous loading by using ITC loaders and Paus Dump Trucks will have sever impact on your KPI’s on Opex, ESG and QSHE.
- Increase of safety
- Energy savings
- Reduce carbon footprint
- Reduced operational cost
- Decrease of time to reach target
- Earlier ore excavation
Benefit | Impact | Countability |
---|---|---|
Eliminate loading Bay Eliminate passing Bay Face work with electric drive |
LHD loading movement reduced to 0, Diesel consumption and Diesel particle reduced, LHD Maintenance reduced, Auxiliary bay blasting accounts up to 20% of your blast time, this can be reduced to 6-10% |
|
Drill & Blast cycle reduction Muck loading, scaling, invert cleaning are 40% of a Drill and blast cycle |
Muck loading, scaling and invert cleaning with one machine, cleaning time reduction by 50% possible, lead to more blast per day |
|
Possible to work on 30% decline | Will allow to change the slope from 9° decline to 13° decline |
Reduction of blasted road meters by 30%, time and cost saving |
Optimize blast pattern to the best blast fragmentation to muck |
Increase the spacing to achieve bigger fragmentation, reduce drill holes |
|
Drill & Blast current systematic
Using LHD as mucking method has several disadvantages
- Need to blast a loading and turning bay for truck and LHD
- Common Truck dimension require passing bays for trucks
- Approx. 20% of blasting time is for auxiliary blasting
- LHD need to travel constantly from face to loading bay
- Diesel consumption for LHD to load muck and travel is high
- Diesel particles are influencing the environment
- Ventilation needs are very high for cooling and cleaning of air
- High risk of accidents due to high movement of LHD
- LHD maintenance cost are based on the travel distances
- Declines need to be designed to accommodate the LHD
- Common decline gradient with LHD/Truck combination is 9°

Focus on the mucking and scaling partvantages
40% of the complete Drill & Blast cycle time for:
- Collecting debris
- Muck loading with LHD
- Scaling with dedicated scaler
- Final cleaning of invert with LHD
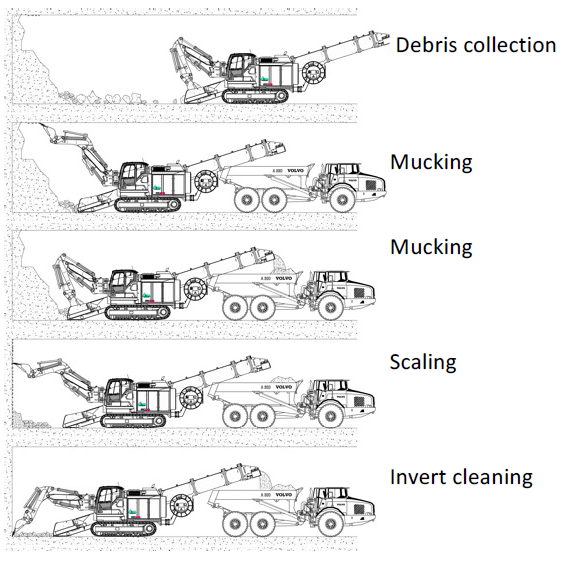
Drill & Blast fast Decline & UG Development
Continuous loading by ITC loader and Paus Dump Trucks
- Implement ITC continuous loading in the D&B cycle
- Eliminate seperate scaling machine
- Increase heading speed
- Increase safety
- Increase block size blast fragmentition for optimized loading and drilling
- Implement Paus Dump Trucks in logistic (Diesel or BEV)
- Reduce or eliminate turning bay
- Reduce or eliminate passing bay
- Eliminate LHD loading of Trucks
Reference: Drill & Blast
- Project Grimsel Switzerland
- 34m2 cross section
- Pull length 3,6 meter
- 4 days each 5 blasts (3 blasts calculated)
- Support 1-2 bolts per meter
- Used wheel loader, 15% gradient
- After 6 month 2 month behind
- Finished tunnel 3 months ahead
- ITC turned the project around
Reference: Drill & Blast
ITC 312 Superloader loading in Breidal, Norway.
The geology in Norway is mainly composed of granite, making drill and blast the most used choice throughout the country.
We currently have 6 machines working there. Most tunnels are between 16m2 to 30m2.
Reference: LHD vs ITC Superloader
Explanation
- Blue : planned heading, orange : LHD loading, green : ITC Superloader
- After only 5 weeks, they were already more than 1 week late with the LHD
- Once the ITC Superloader was there, it took 3 weeks to catch up the planned heading
- They were 2 weeks early on Christmas time
Reference: LHD vs ITC125
After only 80 meters
- In a 21m2 section, our ITC125 + 2 dumpers were faster than 2 LHD after only 80m
- They thought it would be faster after at least 200m
Reference: Case study (Kjøsnesfjorden)
One ITC loader (312N with loading boom H3) + 3x Paus ITC dumpers
Mucking time for 120-130m3 was 60-90 minutes (including scaling and cleaning of the invert)
Expected advancement : around 80m / week
Achieved advancement: 104m / week
Break the Norwegian record for drill and blast advancement with 175.8m in a single week !
«We are very please with the Paus units […] and the ITC loader, they are provinding very close to 100% availability, which is a must of sustaining good production.»
«In the equipment combination, the ITC loader and the PAUS units have proven especially effective.»
Words from the site manager of Kjøsnesfjorden jobsite in Norway
Our machine: made for tunnels
- Continuous, in-line work for more capacity
- High quality component and made in Germany for long durability (oldest machine still in operation : 40 years old !)
Our range of products (1)

The compact machine – from 9m2
- Diesel engine : 80 kW
- Electric motor : 75kW
- Conveyor width : 600mm
- Loading capacity : up to 3m3/min
The Superloader – from 16m2
- Diesel engine : 180 kW
- Electric motor : 132kW
- Conveyor width : 1000mm
- Loading capacity : up to 12m3/min

The medium machine – from 16m2
- Diesel engine : up to 180 kW
- Electric motor : 132kW
- Conveyor width : 800mm
- Loading capacity : up to 6m3/min
The big machine – from 20m2
- Diesel engine : 165 kW
- Electric motor : 110kW
- Conveyor width : 800mm
- Loading capacity : up to 4m3/min
- 2.5 tons hammer
Our goal: maximum efficiency in tunnel
The design of ITC machine is made for the best efficiency while increasing safety from standard excavator
Our machine can perform the following:
- Pure mucking in Drill and Blast drive
- Excavation with a bucket
- Excavation with a hammer or a cutting unit
- Handling block sizes up to 900 mm x 800 mm
- Work on 30% slopes effectively
Tunneling Machines – PAUS Dump Trucks


Sample drawing for exact dimension please request updated drawings info@h-mtec.com

Bi-directional drive


Rear view from the driver seat
- Highest Payload/operating weight ratio of its category
- Only 1900mm wide
- Capacity 22t
- Reversible seat
- Two dumpers can cross easily in a 4.5m wide tunnel
You dream it, we build it
- The M4 boom was made to reach the side of the machine, upward
- The machine was very successful and completed it tasks much faster than a conventional excavator + dedicated loader
- All this with its electric drive
Special Purpose machines and vehicles, designed and known for effective and durable solutions.
All machines are designed to meet the challenging tasks at the underground. Besides a wide choice of standard equipment and configurations already available all machines can be customized to your needs or even newly-developed to meet your individual demands.


Special-purpose machines and vehicles
Hermann Paus Maschinenfabrik GmbH develops and produces special-purpose machines and vehicles for special applications in tunnel construction and mining as well as for the areas of lift technology, construction machines and industrial vehicles.

A problem solver
Our products have made a name for themselves as a problem solver in the industrial sector and trades – in both domestic and international use. Paus represents “Quality made in Germany”. Our remote controlled scaler, explosive charger, full set of utility vehicles, loaders and Dump Trucks are well designed for the use in the South African Market.

Battery electric vehicles
Including mobile equipment such as working platforms, explosive transporters and chargers, scaler, grader, LHD loaders, dump trucks, personnel carrier, concrete mixers and spraying machines, rescue vehicles and many more.

Made for miners
One of the main features of our Dump Truck portfolio is their compact size. They fit perfect in small veins and low seams and are highly requested due to their possibility of passing each other with out blasting a passing bay. Their bi-directional driving capabilities do not require a turning bay what makes the planning of underground development areas much compacter and more cost effective.